Refurbishing and retrofitting of multi-spindle lathes
The retrofitting of multi-spindle lathes is a meticulous and detailed process that allows us to give a future to those machines that, according to most, have reached the end of their life, but which are the foundation for new and stimulating projects for us.
It all starts with an in-depth interview with the customer: We need to understand what their production needs are to guide them in choosing the machine that fits them perfectly. Starting from the technical drawing of the workpiece and the work cycle, we determine all the details necessary to optimize the machine and the user experience.
Ready, set, go: The complete disassembly of the machine is the first stage of our retrofitting process. This way we can assess the initial shape of the machine in detail.
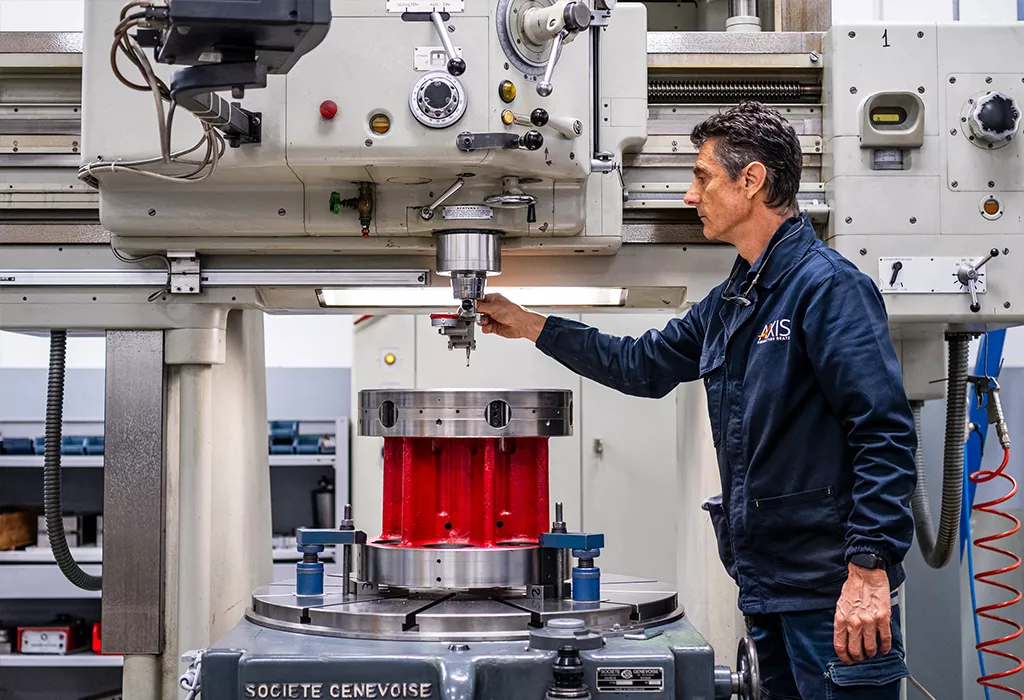
Once everything has been tested, what shall we start with, if not the heart of the machine? The drum and its seat in the upright are tested and then refurbished according to a precise protocol: thanks to our SIP GENEVOISE department and our experts, we can develop and generate the new housing in which the ground drum will be located to guarantee coupling within a tolerance of 0,001 mm. To ensure the greatest working accuracy, we also check and, if needed, restore, the six or eight spindle housings.
Once everything is aligned, and geometric tests show that the structure and the heart of the lathe comply with our standards, we continue with the assembly of all the other parts of the machine.
In this second part of the process, our fitters install all the assemblies and make sure that the tolerances of all mechanical couplings are restored, thanks also to close cooperation with our grinding department. All worn components are replaced with new ones.
But if that were enough, it would be too easy. We don't just want to get the machine back to its best former condition, we want to make it even better. The technical department and the fitters cooperate and study how to improve the existing components and develop new equipment and accessories to make them much better than originally designed. This way, we manufacture a unique, modern and customized machine that meets the customer’s exact needs.
Once the assembly process is complete, we finish the work by building and painting the new guards in our dedicated department.
When the machine is ready, all we have to do is bring it to life: with the help of the electricians who have installed the new electrical system, our software developers work to finalize the project thanks to PLC or CNC units, either Fanuc, Mitsubishi or Siemens.
Contact us for more information or a personalized quote
Our strength lies in carrying out the feasibility analysis together with our customers, then recommending the best technology that suits their needs.
Fill out the form to submit your need to us and we will find the best solution together.